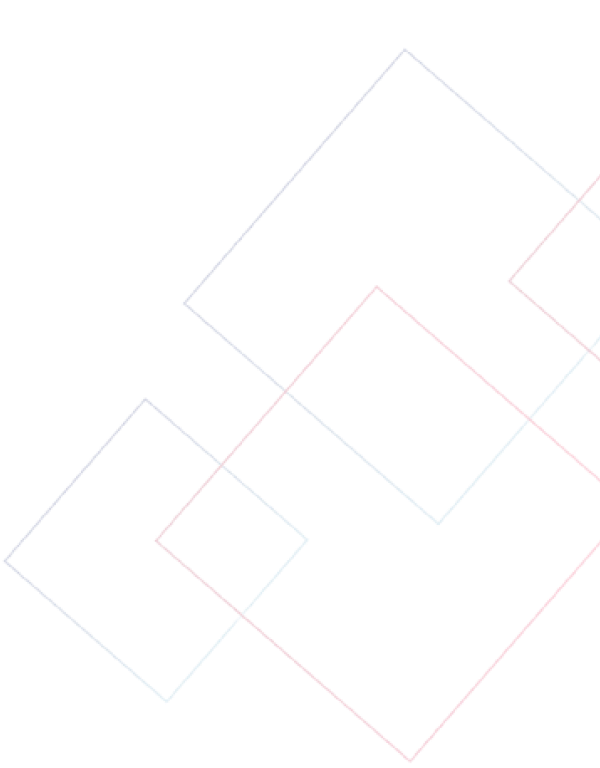
探秘中空玻璃生产线:高效生产背后的奥秘
时间:2025-01-25 来源:http://www.jncsjx.com/ 发布人:昌盛机械
在建筑行业蓬勃发展的今天,节能、环保、舒适成为了建筑设计的重要追求。中空玻璃作为一种具备卓越隔热、隔音性能的建筑材料,在现代建筑中得到了广泛应用。而中空玻璃生产线,作为实现中空玻璃高效、高质量生产的关键设备,其技术和工艺的发展也备受关注。
In today's booming construction industry, energy conservation, environmental protection, and comfort have become important pursuits in architectural design. Hollow glass, as a building material with excellent thermal and sound insulation properties, has been widely used in modern architecture. As a key equipment for achieving efficient and high-quality production of insulating glass, the development of technology and processes in the production line of insulating glass has also attracted much attention.
一、工作流程全解析
1、 Complete analysis of workflow
玻璃原片切割:根据生产需求,将不同规格的玻璃原片通过切割设备按照精确尺寸进行切割。切割设备配备高精度的测量和控制系统,确保切割尺寸的准确性,误差控制在极小范围内。例如,在大型建筑项目中,对于门窗玻璃的切割尺寸要求严格,生产线的切割设备能够依据设计图纸,将玻璃原片精准切割成所需大小,为后续加工奠定基础。
Glass wafer cutting: According to production needs, glass wafers of different specifications are cut into precise sizes using cutting equipment. The cutting equipment is equipped with a high-precision measurement and control system to ensure the accuracy of cutting dimensions and control errors within a very small range. For example, in large-scale construction projects, strict requirements are placed on the cutting size of door and window glass. The cutting equipment on the production line can accurately cut the glass into the required size based on the design drawings, laying the foundation for subsequent processing.
清洗与干燥:切割后的玻璃进入清洗干燥环节。清洗机采用高压喷水和毛刷相结合的方式,彻底清除玻璃表面的灰尘、油污等杂质。清洗过程中,水循环系统对清洗用水进行过滤和净化,实现水资源的循环利用,既环保又降低生产成本。清洗后的玻璃通过热风吹干或真空风干技术,确保表面无水渍残留,避免在后续加工中产生质量问题。
Cleaning and drying: The cut glass enters the cleaning and drying process. The cleaning machine uses a combination of high-pressure water spray and brushes to thoroughly remove dust, oil stains, and other impurities from the glass surface. During the cleaning process, the water circulation system filters and purifies the cleaning water, achieving the recycling of water resources, which is both environmentally friendly and reduces production costs. The cleaned glass is dried by hot air blowing or vacuum air drying technology to ensure that there are no water stains left on the surface and avoid quality problems in subsequent processing.
间隔框制作与填充:利用专用设备将铝条或其他材质的间隔框按照规定尺寸进行折弯成型。在折弯过程中,设备通过模具和精确的机械控制,保证间隔框的角度和尺寸精度。随后,在间隔框内填充干燥剂,干燥剂能够有效吸附中空玻璃内部的水分,防止在使用过程中出现结露现象,确保中空玻璃的隔热和隔音性能。
Space frame production and filling: Use specialized equipment to bend aluminum bars or other materials into space frames according to specified dimensions. During the bending process, the equipment ensures the angle and dimensional accuracy of the spacer frame through molds and precise mechanical control. Subsequently, a desiccant is filled in the spacing box, which can effectively absorb the moisture inside the insulated glass, prevent condensation during use, and ensure the insulation and sound insulation performance of the insulated glass.
合片与密封:将干燥后的玻璃与制作好的间隔框进行合片,通过机械定位和压紧装置,使玻璃与间隔框紧密贴合。接着进行第一道密封,通常采用涂丁基胶的方式,丁基胶具有良好的密封性和耐候性,能够有效阻止空气和水分的进入。第一道密封完成后,进行第二道密封,根据不同的使用场景和性能要求,选择聚硫胶或硅酮胶等密封材料,进一步增强中空玻璃的密封性能和结构稳定性。
Splicing and sealing: The dried glass is laminated with the pre made spacer frame, and the glass is tightly adhered to the spacer frame through mechanical positioning and compression devices. Next, the first sealing is usually done by applying butyl rubber, which has good sealing and weather resistance, and can effectively prevent air and moisture from entering. After the first sealing is completed, the second sealing is carried out. Depending on different usage scenarios and performance requirements, sealing materials such as polysulfide or silicone adhesive are selected to further enhance the sealing performance and structural stability of the insulated glass.
质量检测:完成密封后的中空玻璃进入质量检测环节。通过人工目检和专业检测设备相结合的方式,对中空玻璃的外观、密封性能、尺寸精度等进行全面检测。外观检测主要检查玻璃表面是否有划伤、气泡、杂质等缺陷;密封性能检测则通过压力测试等方法,确保中空玻璃的密封效果符合标准要求;尺寸精度检测使用高精度测量工具,对中空玻璃的长、宽、厚度等尺寸进行测量,保证产品尺寸的准确性。只有通过严格质量检测的产品才能进入下一环节。
Quality inspection: After sealing, the insulated glass enters the quality inspection process. Through a combination of manual visual inspection and professional testing equipment, the appearance, sealing performance, dimensional accuracy, and other aspects of insulated glass are comprehensively tested. Appearance inspection mainly checks whether there are scratches, bubbles, impurities and other defects on the glass surface; The sealing performance testing is carried out through methods such as pressure testing to ensure that the sealing effect of the insulated glass meets the standard requirements; Dimensional accuracy testing uses high-precision measuring tools to measure the length, width, thickness, and other dimensions of insulated glass, ensuring the accuracy of product dimensions. Only products that have passed strict quality testing can proceed to the next stage.
包装与储存:合格的中空玻璃进行包装,通常采用塑料薄膜或纸质包装材料,对玻璃进行保护,防止在运输和储存过程中受到碰撞和损坏。包装好的中空玻璃按照规定的方式进行堆放和储存,储存环境要求干燥、通风,避免阳光直射和潮湿环境,以确保产品质量的稳定性。
Packaging and Storage: Qualified insulated glass is packaged, usually using plastic film or paper packaging materials to protect the glass from collision and damage during transportation and storage. Packaged insulated glass should be stacked and stored in a dry and ventilated environment according to regulations, avoiding direct sunlight and humid conditions to ensure the stability of product quality.
二、关键技术亮点
2、 Key technological highlights
自动化控制技术:现代中空玻璃生产线广泛应用自动化控制技术,通过 PLC(可编程逻辑控制器)和触摸屏等设备,实现对生产过程的精确控制和监控。操作人员只需在触摸屏上输入生产参数,如玻璃尺寸、加工工艺等,生产线即可自动完成各项加工任务。自动化控制技术不仅提高了生产效率,还减少了人为因素对产品质量的影响,保证了产品质量的一致性和稳定性。
Automation control technology: Modern insulated glass production lines widely use automation control technology to achieve precise control and monitoring of the production process through devices such as PLC (Programmable Logic Controller) and touch screens. Operators only need to input production parameters such as glass size, processing technology, etc. on the touch screen, and the production line can automatically complete various processing tasks. Automated control technology not only improves production efficiency, but also reduces the impact of human factors on product quality, ensuring consistency and stability of product quality.
高精度定位技术:在合片、密封等关键工序中,高精度定位技术起着至关重要的作用。生产线采用先进的传感器和机械定位装置,能够将玻璃和间隔框准确地定位在预定位置,确保合片的精度和密封的质量。例如,在合片过程中,通过视觉传感器对玻璃和间隔框的位置进行实时监测和调整,使两者的贴合误差控制在极小范围内,从而提高中空玻璃的整体性能。
High precision positioning technology: High precision positioning technology plays a crucial role in key processes such as lamination and sealing. The production line adopts advanced sensors and mechanical positioning devices, which can accurately position the glass and spacer frame in the predetermined position, ensuring the accuracy of lamination and the quality of sealing. For example, during the lamination process, the position of the glass and the spacer frame is monitored and adjusted in real time through visual sensors, so that the bonding error between the two is controlled within a very small range, thereby improving the overall performance of the insulated glass.
节能环保技术:随着环保意识的不断提高,中空玻璃生产线也越来越注重节能环保技术的应用。在清洗环节,水循环系统和高效过滤装置实现了清洗用水的循环利用,减少了水资源的浪费;在干燥环节,采用高效节能的干燥技术,如真空风干、热回收干燥等,降低了能源消耗。此外,生产线在设备选型和设计上,也充分考虑了节能因素,采用低能耗的电机和先进的传动系统,降低了整个生产过程的能耗。
Energy saving and environmental protection technology: With the continuous improvement of environmental awareness, the production line of insulating glass is also paying more and more attention to the application of energy saving and environmental protection technology. In the cleaning process, the water circulation system and high-efficiency filtration device achieve the recycling of cleaning water, reducing the waste of water resources; In the drying process, efficient and energy-saving drying technologies such as vacuum drying and heat recovery drying are used to reduce energy consumption. In addition, the production line has fully considered energy-saving factors in equipment selection and design, adopting low-energy motors and advanced transmission systems to reduce the energy consumption of the entire production process.
三、维护保养要点
3、 Key points of maintenance and upkeep
机械部件维护:定期对生产线的传动部件,如链条、链轮、皮带等进行检查和维护,确保其润滑良好、张紧适度,避免出现松动、磨损等问题。对各传送辊、毛刷辊的轴承进行定期加注润滑
Mechanical component maintenance: Regularly inspect and maintain the transmission components of the production line, such as chains, sprockets, belts, etc., to ensure good lubrication, moderate tension, and avoid problems such as looseness and wear. Regularly lubricate the bearings of each conveyor roller and brush roller
- 全自动铝条折弯机技术在哪方面提升了 2025/04/19
- 全自动封胶线有什么技术优势? 2025/04/18
- 中空玻璃生产线成本高,怎么选性价比高的? 2025/04/15
- 验收时才发现玻璃自爆,工期延误赔偿百万? 2025/04/14
- 中空玻璃加工设备的讲解 2025/04/12
- 毛刷式清洗机怎么使用 2025/04/11
- 中空玻璃加工设备核心是什么? 2025/04/10
- 全自动铝条折弯机如何设置更快,让编程更简单? 2025/04/09
- 双组份打胶机让胶水发挥最大威力 2025/04/08
- 卧式丁基胶涂布机的优势有什么 2025/04/07